Sriperumbudur, a quiet town outside of Chennai, is now increasingly known for its sprawling automobile factories, electronic SEZs(Special Economic Zones), and of course, hot job opportunities. Several automobile and mobile phone giants are part of this story. It all started 10 years back, when automobile companies like Hyundai saw the proximity to a harbour huge enough to handle exports and set up bases here, quickly gaining this city the name “Detroit of India”.
In the same “Detroit of India” lies one of Nokia’s biggest production facilities. The opportunistic Nokia of the past saw the booming mobile market in India in the 2000s, and started setting up their assembling facility here, right in the heart of Sriperumbudur’s SEZ. The logistics for exports had already become robust, thanks to the omnipresent automobile industry in that area, so the opportunity was ripe.
On a surprisingly overcast day, I was on my second visit to Nokia’s Chennai facility with several other bloggers. Having already witnessed the marvel of a huge production facility the first time, I couldn’t wait to see what new tricks Nokia had up their sleeves. Spoiler: It’s the Nokia Asha 501.
Yes, the Nokia Asha 501 is one of the many devices that are in production at its Chennai facility. Launched worldwide at an extravagant event in New Delhi, the Asha 501 was a fresh entrant into the low end market, with several aspirational high end features and an ambitious software reboot. According to Ritchie Rice, Senior Manager at the Nokia facility in Chennai, the device has been in production for quite some time, to meet the ongoing local demand.
Dressed in appropriate factory style clothing(lab coats and all) with a weird sock over our shoes, we set foot into territories usually out of bounds for visitors. The Chennai facility is more of assembling than manufacturing, says Ritchie, acknowledging the fact that silicon level production equipment is very hard to procure, and hence are left with component manufacturers to deal with. That said, the equipment used for assembling is no less in complexity, which we figured out after entering the massive factory floor to witness how the Asha 501 was made.
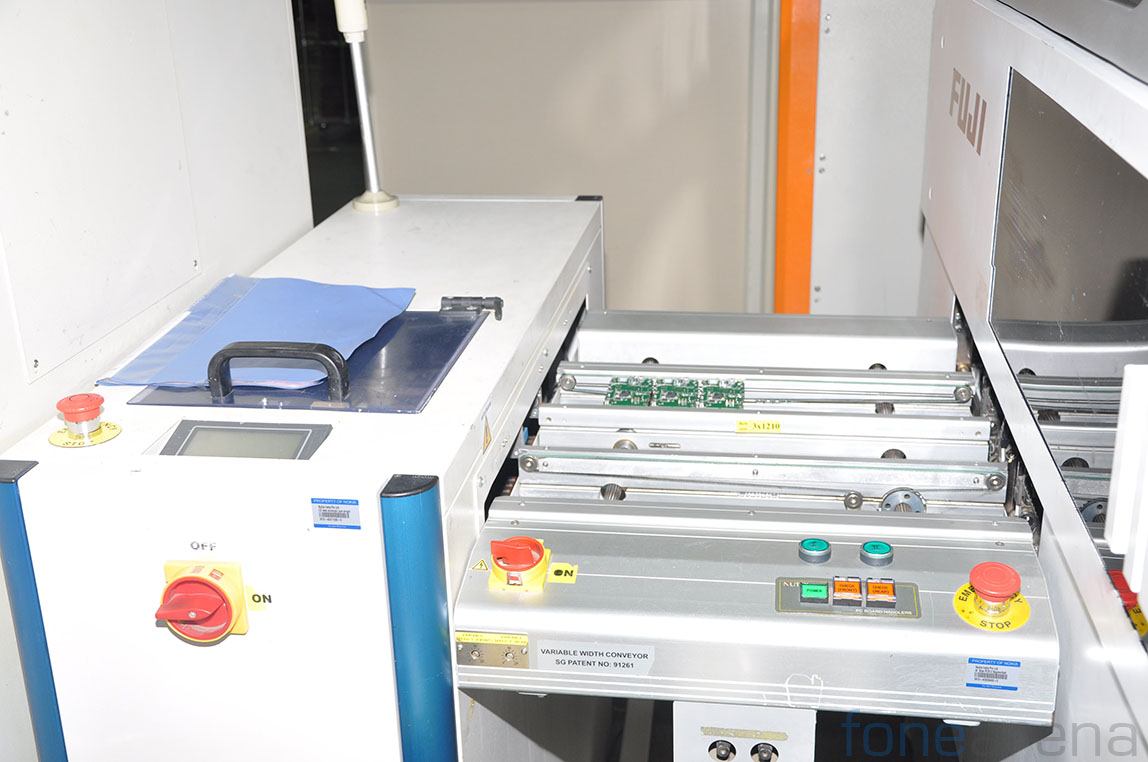
It started with the bare circuit boards that were already procured from the component suppliers. These were stacked up and ready to be deployed in what they call a “production line”. This line is a series of equipments that are capable of handling automated tasks that are related to precise component installation on to the circuit board. The first series of equipments prepare the board with adhesives in proper temperature. The board then goes through several equipments loaded with small components in long plastic strips. The officials said that these strips each have a custom component specific for the Asha 501 and are acquired from the nearby component suppliers in the same SEZ.
Once the components are affixed, the Asha 501′s board goes through a manual process of placing the camera unit on the board.
Yes, the line is not completely automated unlike what we had imagined, and Ritchie said it is usually the case with most workflows. Once the camera is placed, it then goes through some small quality checks for board level burns or other physical aberrations.
Once the process is done, the boards are stacked in a plastic rack and moved for other stages of assembling.
The display and the touchscreen units are then placed on to the boards, which then proceed to be fixed on to the plastic chassis. This is all done manually, by the employees. Interesting fact is that more than 50% of the Nokia employees at the facility are women. Nokia are really proud of this fact and boast several other initiatives for the uplifting of the locals and their culture. For example, Nokia funds a group(a NGO) that strives to protect the ancient art of silk weaving in Kanchivaram, a nearby district that’s world famous for its silk sarees. Through initiatives like these, Ritchie says Nokia has inadvertently impacted their employees’ lives.
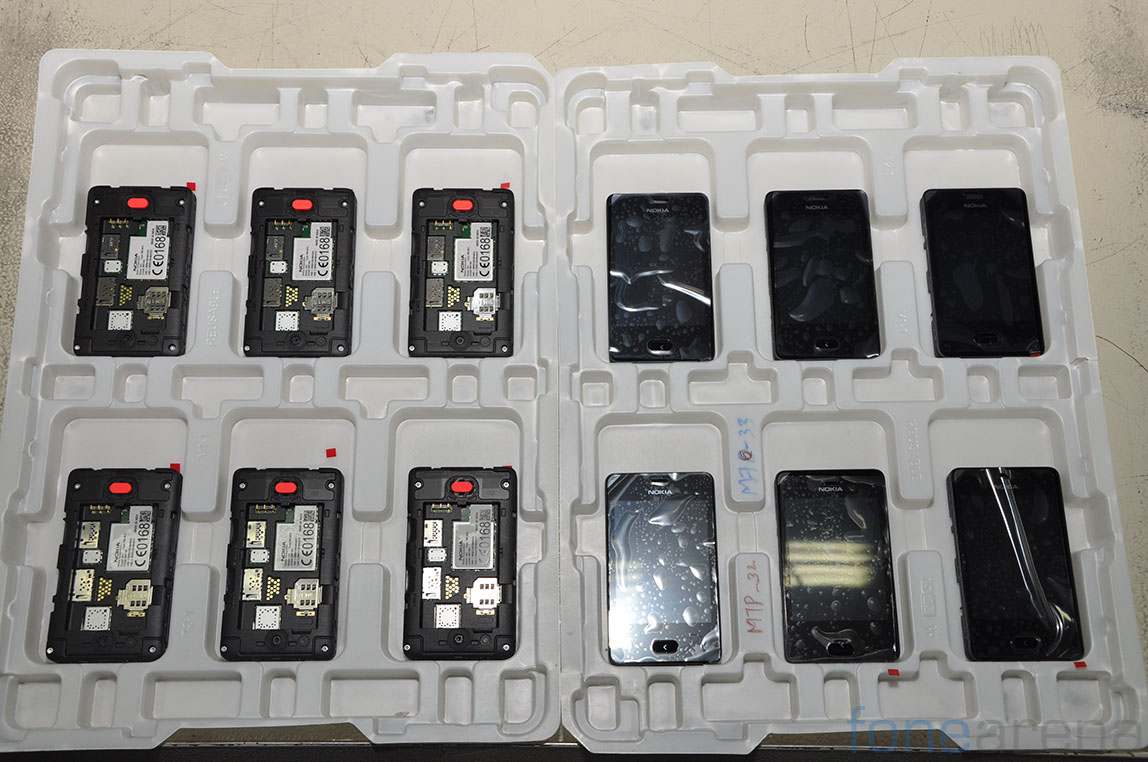
Coming back to the plastic chassis of the Asha 501, I was particularly interested in knowing what Nokia does, for the plastic cases. Especially whether they are imported, or locally procured. I was really curious because of the quality of the Asha 501′s shells, and even the colours that ran deep. I was told that they were indeed sourced locally, and I was told that Chennai has really good plastic suppliers. It was also curious to note that they usually don’t rely on a single supplier for any crucial component, as the production is too important to be stopped on the basis of supply issues. I also noted this separate counter for the red coloured earphones, which go in every Asha 501 box irrespective of its colour.
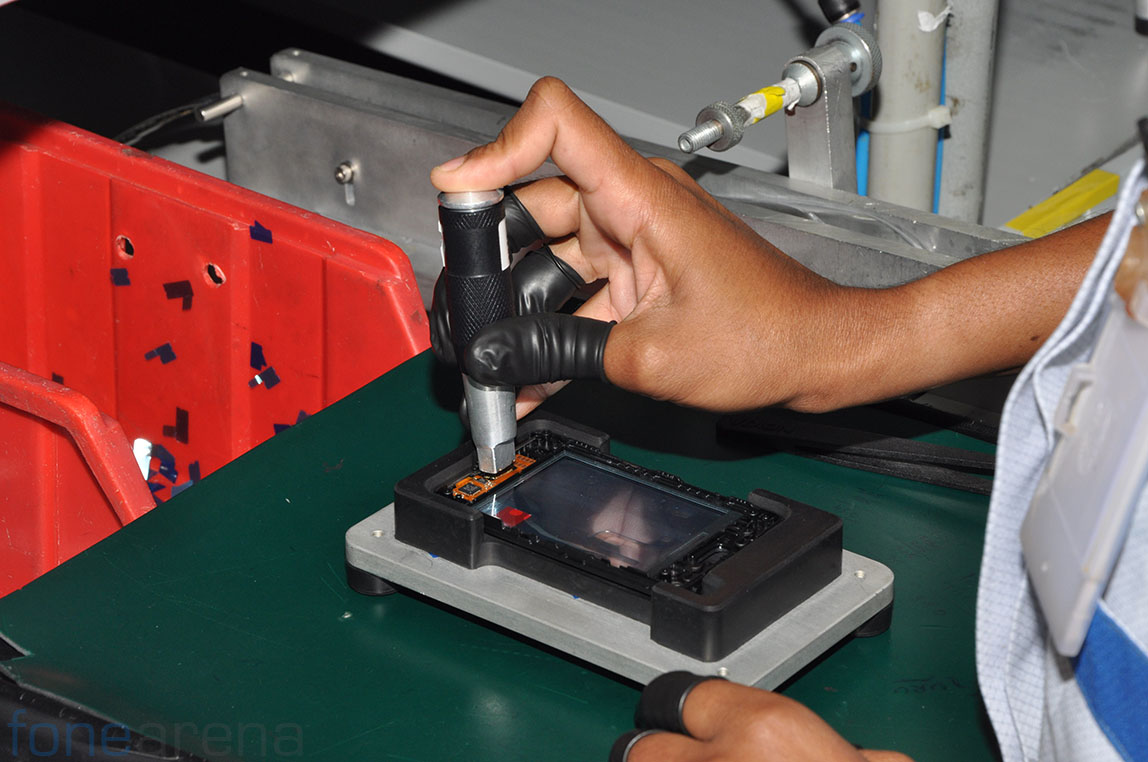
Once the assembling of the phone is complete, it then heads on to the software loading and testing part and finally the packaging where the IMEI is fixed and box contents are packed. We noted that the 4GB micro SD card that comes pre installed with the Asha 501 is actually inserted in the phone before packaging. Once the packaging is done, it heads for shipment. But where’s the testing you ask?
Here’s where things get a little bit interesting, well at least for us as spectators. So, Nokia has all kinds of torture tests arranged in its own testing chambers. You have a dusty tumbling unit that continuously rolls the device up and down with dirt, a drop test that slams the phone on a concrete slab at high speed, a button consistency test with it poking the hardware buttons for hours and days at stretch and even a humidity test with the phone in a chamber of extreme manipulated weather conditions. To be honest, it was really exciting to see all the equipment and the testing going on at the “torture” chamber. We were told that a select batch of devices from each shipment goes through this strenuous testing every day.
In the end, we headed for a small Q&A with Ritchie Rice in which my immedaite question was “Why Chennai?”. Ritchie explained to me that the Asha 501 is currently manufactured in three locations across the world, one being the Chennai facility. The Asha 501 comes in dual SIM as well as single SIM variants, and as the Chennai facility is already tooled for the dual SIM devices, it made sense for them to manufacture that variant here, he said. It is also for catering to the local demand, as logistics of pushing the device through the Indian distributors made much more sense to do it from Chennai than abroad, said Ritchie.
So, obviously our next question was “When will Lumias be made here..?”. It was obvious that it has not been considered yet for the facility, not because of the complexity of the equipment or the ability to procure materials, but just due to the demand. Apparently, Nokia’s shipments in India still largely lie in the low end and it makes a lot more sense to push these devices locally than the Lumias. Honestly, it made sense for us, but as the smartphone market rapidly expands even further, may be Nokia will consider.
That concludes my experience at the Nokia Chennai factory. It was really interesting to see how the mobile devices are constantly churned out and even exported globally right from a city in India, which actually makes Nokia as much an Indian company as the local ones that claim to be. The Asha 501 Dual SIM is surely made in India, by Indians and for India. Do
read our review for a complete look at the device, and let us know if you have any questions about our visit, in the comments section below.